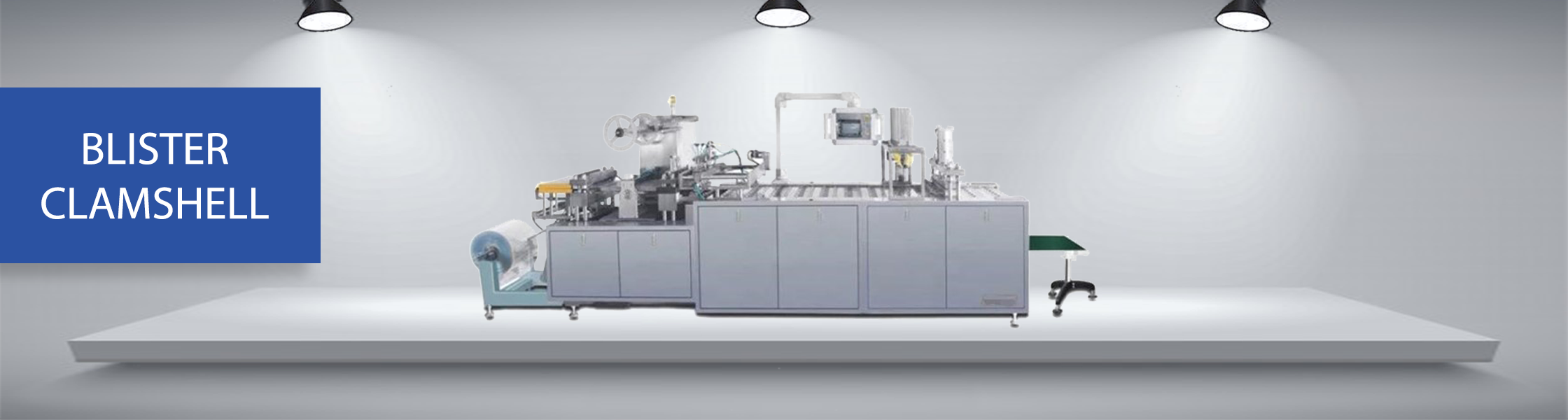
Blister | Clamshell Packaging Machine
Packaging Video
Clamshell packaging is a form of blistering packaging that is designed with two clear plastic sections that are joined with a hinge on a centerline. Both sections can fold open and interlock like a clam to create an enclosed container around a product. These packages are ideal for protecting, containing, transporting, and displaying single items on pegs or shelves, depending on packaging design.
Our Packaging Machines USA Ranges
Our Clamshell Blister packaging machines cover a wide variety of applications and can be customised according to your production needs. All individual modules that comprise our clam blister packaging machine options are available in automatic and semi-automatic versions according to your production requirements.
Since clam packaging works best for products that won’t fit into conventional blister packaging, clamshell blister packaging machines are commonly used for the packaging of goods that come in a set of variable sizes like tool sets, gift sets, cosmetics, etc.
Other consumer goods like food, fresh produce, candy, smartphones, hardware, electronics, higher-value items like professional golf and squash balls, and medical supplies can be packaged this way.
- Single-piece, buttoned packaging design allows for easy opening and closing for display purposes
- Safe and efficient sealing of PVC, PETG, GAG, PET and similar materials is ideal for high- volume OEM’s and contract packagers
- End results are usually clear, tamperproof, stackable clamshell blister packs that are visually appealing to the end-user and very hard to steal due to their often-unusual shapes
- Hermetically sealed clam packs offer optimal gas flushing to preserve produce shelf life
- Reduced labour costs since machine can be fully automated with auxiliary equipment used to denest, top-seal, close and/or label packaging
- Versatile range of sealable plastics that can be shaped to hold virtually any type of product
- Twin push controller, teflon scroller, specialised match plate, aluminium tooling, auto-indexing guide and semi-automatic sealer included as standard
- Efficient packaging capacity of 6-12 cycles per minute
- Reduced transports costs due to lightweight packaging mass
- Clamshell packaging is easily recyclable and particularly useful in shorter packaging runs
- Intelligent PLC touch screen interface with heavy-duty cam indexer and AC variable frequency drive
- Carousel and inline machines allow for additional open loading stations, automatic vibrating feeders, and robotic placement arms
- Heavy-duty industrial design ideal for high volume packaging lines
Designed for medium to higher volume production lines, clamshell packages are formed using various forms of clear plastic like HIPS, PVC, PET and recycled PET, PETE, PETG, PP, and Polyurethane through a process called thermoforming.
Thermoforming refers to a process of heating rigid plastic sheets into a malleable form and cooling it back into a rigid state around a mould with the use of a vacuum. Thermoformed webs are pliable enough to be formed into virtually any shape.
A reel of stock film web is initially fed through a predefined cavity former called the blister forming unit. Once the blister has been formed, a guiding track moves the web to the filling station. Here, individual blisters are automatically filled with a product before the web enters the sealing unit.
Conventional sealing units feature a heated sealing station, a cooling station, a package unload station, a bottom blister feed station as well as an insert card feed station, a top blister feed station, and two extra stations used for product loading.
When the web is in place, a separate reel of aluminium foil is fed into the sealing unit where it is hermetically sealed to the base web. Rotary heat sealers, on the other hand, usually come with optional automatic card-feeding and package discharge systems that are freestanding or a permanent fixture depending on machine design.
Once sealed, the web moves on to the pack punch unit where packs are separated from the web with the help of an indexing mechanism. Excess web trim is cut away and collected. Finished clamshell packs are then either collected in large containers or transported on a conveyor belt for further handling. Clam packs can also have studded seals that press together and pull apart like buttons.
Clamshell packaging machines can be linked to a cartoner, and a chilling station can be installed to eliminate the need for routing in-plant chilled water to the machine. Casters, and lightweight package hold-down systems also offer greater versatility.
Packaging Application
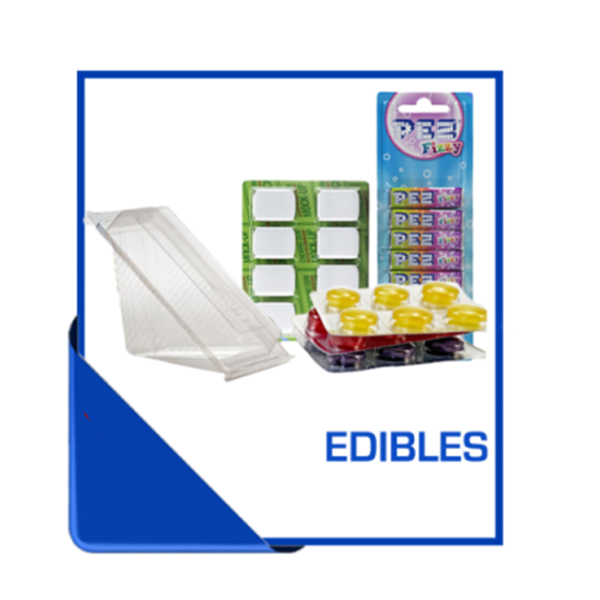
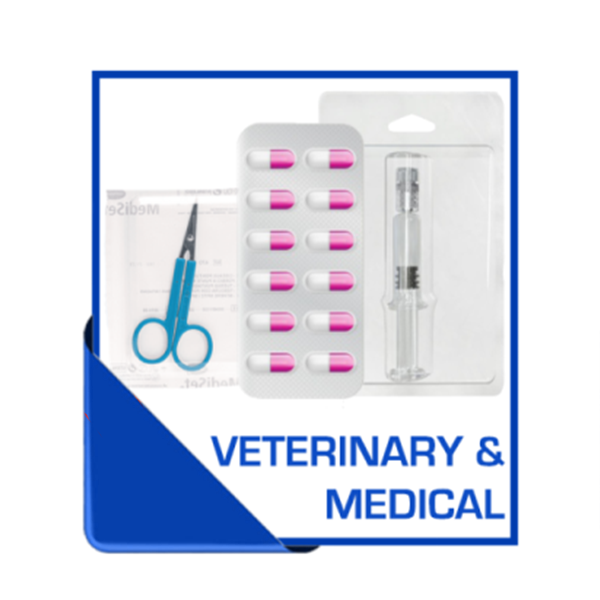
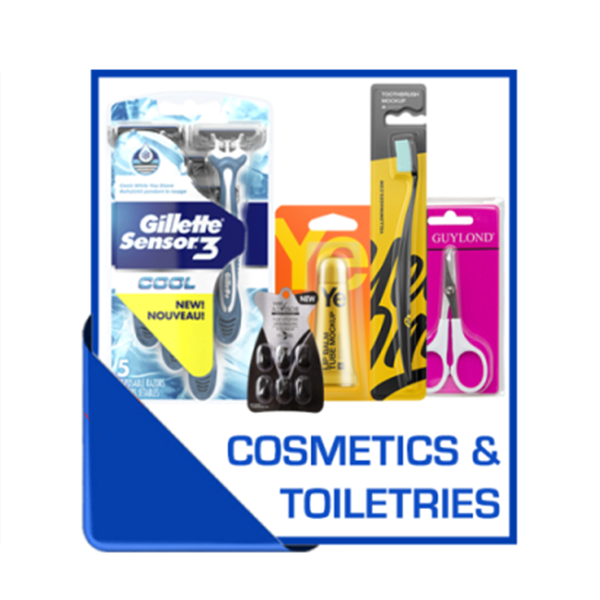
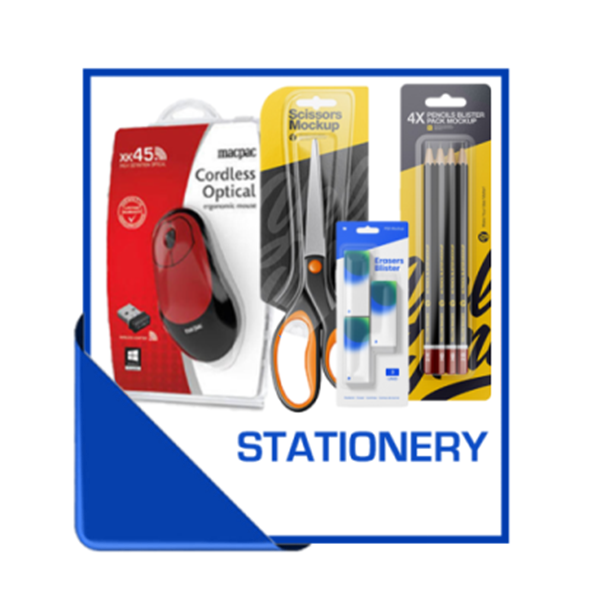